         
|
� |
�
Johnstown Recycling Ltd
- New Organic
Composting Facility
Johnstown
Recycling have announced the opening of their new Organic Composting
Facility at Slanemore just outside Mullingar.
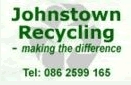
The new facility is the only one of its kind in the midlands, in
so far as it organically recycles all biodegradable waste - including
Food Waste - and turns it into compost. The company is fully
licenced to accept food waste, cardboard, green waste and paper
- and uses an In Vessel system, which meets all European Union regulations.
With an increasing emphasis on environmentally safe methods of
waste disposal, it is clear that the new operation is a unique opportunity
for a range of businesses - e.g. hotels, restaurants, supermarkets,
etc - to safely and legally dispose of kitchen waste.
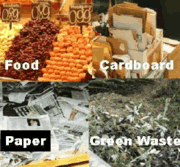 |
Over the next few years, under EU legislation, disposal of
biodegradable waste will no longer be accepted by landfill
- and will, necessarily, be sent to a recycling or composting
facility.
This new method of waste disposal will be more cost-effective
than the present system of landfill use.
In this regard, Johnstown Recycling has structured its operation
so that, not only can the waste be collected from clients'
premises - but the company's charges have been held at extremely
competitive levels.
|
Composting System
The CCS composting process at the Johnstown facility consists of
the following steps -
|
Feed-stock blending in a mixer; |
|
Initial high-rate composting within enclosed tunnels; |
|
Screening to remove oversized, undecomposed materials
and contaminants; |
|
Storage until the compost is blended, packaged
and/or delivered to users. |
The CCS composting process begins with the blending of clean source-separated
feed-stock materials to achieve the proper balance of nutrients,
moisture and porosity for optimal composting. The CCS in-vessel
composting system is a computerised tunnel composting system.
The in-vessel system is used for the initial processing of
materials within an enclosed environment - so that odours
and leachate can be completely contained and controlled, temperatures
manipulated and vermin excluded. The in-vessel system utilises
a computerised process control system to regulate airflow
through the composting tunnels - via a temperature
feedback cycle.
The computer system is set up to log critical data, so that
regulatory standards for temperature monitoring and reporting
can be easily met. All process air from the in-vessel system
is forced through biofilters to remove odours.
|
|
Once materials have been stockpiled for a prolonged period of time,
they are screened to retrieve bulking materials - such as wood chip
- in addition to large physical contaminants - such as plastic,
rocks, metal cans and other inert matter. Once screened, the finished
compost can be stored until it is delivered in bulk to end-users
- or is blended with other materials to produce bulk or bagged topsoil,
potting soils, organic fertilisers or custom growing media and delivered
to markets for sale.
Materials Mixing
An auger mixer, powered by a farm tractor or front-end loader's
power take-off unit can be used to mix various feed-stock materials
into a homogeneous blend. The auger mixer comes equipped with a
scale, so that the different feed-stocks and bulking materials can
be blended according to these recipes by weight and volume.
|
Factors to be controlled in the mixture include - nitrogen,
carbon, moisture, particle size, microbial inoculation and
porosity or free air space.
Once a proportionate batch is created, the blend is left
in the mixer until fully homogenized. This takes approximately
5-10 minutes.
The blend, suitable for composting, is then transferred into
the loading bay section by conveyor.
|
Other methods of material mixing and blending can be used - such
as simple turning with a front-end loader or blending - using a
specialised blending bucket.
In-Vessel Tunnels
Initial composting occurs within the CCS in-vessel tunnels. These
concrete tunnels are 10 metres long by 5.5 metres wide, with a composting
mass height of between 2 and 2.2 metres - giving a capacity of approximately
120 cubic metres. Loading occurs with the opening of one of the
two hinged steel doors at either end of the tunnel.
The tunnels have numerous aeration grates embedded in the floor,
which are connected to a series of aeration pipes buried in the
concrete floor. This allows air - blown into the bottom of the tunnel
- to permeate through the composting mass. An exhaust duct is located
in the tarpaulin roof to draw process air out of the tunnel with
the use of another blower and force it through a biofilter. The
doors are sealed with a watertight gasket and the tarpaulin roof
is bolted tight to the tunnels walls with a rubber gasket to ensure
a sealed roof. When it is time to unload the composting materials,
the unloading door is opened and the loading shovel drives into
the tunnel and removes the material.
All leachate generated in the process is collected in the
aeration piping system, which doubles as a leachate collection
system and makes its way to a storage tank through the leachate
piping network.
The tunnel doors are lined with a high-density epoxy coating
on the interior and painted with epoxy paint on the exterior
to prevent corrosion.
Two access ports for inserting the RTD temperature probes
are located in the unloading door to allow for temperature
measurement at both ends of the pile.
|
|
Process Control System
The CCS in-vessel system comes with a personal computer (PC) - using
Windows XP operating software that is networked to a programmeable
logic controller (PLC). Inputs to the PLC are listed according to
each tunnel, which can be monitored individually or for each tunnel.
Input data include temperature, variable speed drive efficiency
and airflow rates.
|
Temperature is registered on the Celsius scale
and airflow rate is registered as a percentage of the blower
capacity. Data logging trends include tunnel identification,
blower speeds, variable frequency drive (VFD) efficiency and
temperature.
Temperature logs are stored on the hard-drive as a data-base
file (DBF) for each tunnel and each batch of compost. The PC
itself is linked to a modem, which allows remote monitoring
of the system and alterations to process variables by named
operators. |
Aeration System
The in-vessel tunnel system has a positive and negative blower for
each tunnel - both of which are controlled by variable frequency
drives that are modulated to maintain a differential pressure on
the system.
Material Receipt
The following provides a list of acceptable and non-acceptable materials
in the incoming loads.
Acceptable
|
Not Accepted
|
Garden
Materials:
Lawn clippings
Leaves
Old plants
Cut flowers
Tree primings
Weeds
Shrub trimmings
Wastewater Sludges
Food based Sludges |
Garden
Materials:
Rocks
Litter
Broken tools
Garden machinery
Used garden furniture
Empty oil, pesticide or fertilizer containers
a a a aaaaaaaaaaaaaaaaaaaaaaaaaaaa
aaaaa
aaaaaaaaaaaaaaaaa
aaaaaaaa |
Kitchen
Materials:
Vegetables
Fruit
Tea bags
Coffee grinds and paper filters
Pasta and rice
Cereals
Plate scrappings
Bread
Meat and bones
Egg shells
Cheese
Fish skin and bones
Paper napkins and towels
Cereal, cracker and biscuit boxes (no plastic liners)
Paper egg cartons
aaa
aaaaaaaa
aaaa
|
Kitchen
Materials:
Plastic bags
Sweet and crisp wrappers
Food tins
Beer and mineral cans
Household batteries
Cutlery
Milk cartons
Crockery
Light bulbs
Plastic yogurt containers
Glass jars
Plastic meshing
Styrafoam cups, plates or bowls
Old pots and pans
Aerosol cans
Tin or aluminum foil
Plastic butter or margarine tubs
Plastic milk bottles
Mineral bottles |
For further information, contact -
Michael Dolan
Johnstown Recycling
Tel: +353 (0)44 9373032
Mob: +353 (0)86 2599165
Email: [email protected]
Web: www.johnstownrecycling.com
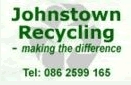
�
|
|