�
Powerscreen Recycling
Plants "produce the goods" for McKinstry Skip Hire
�
McKinstry Skip Hire is a family owned business,
founded in 1969 by Albert "Tiny" McKinstry - who now has his
sons Mark and Darren working alongside him in this well-established
Crumlin based company.
"Tiny" and his sons have seen many changes in
the skip hire business over the past few years - not least
of which was the effect of the introduction of landfill tax.
It was this event that brought about a whole new thinking
in respect of waste treatment, management and landfill disposal
and McKinstry Skip Hire were quick to realise the considerable
advantages - both economically and environmentally - of recycling
and reclamation of the not inconsiderable annual tonnage that
their huge fleet of skips and roll-on-off containers was handling.
An initial investment in a Powerscreen screening
plant some 9 years ago saw the beginning of a close and mutually
advantageous business relationship between McKinstry Skip
Hire, Powerscreen International and their dealer - McGurk
Screening Systems. This fine working partnership continues
today, with McKinstry investing in new Powerscreen equipment
and associated conveying systems from McGurk. McKinstry Skip
Hire will be taking a new and enhanced prototype version of
the Powerscreen Trommel 725 for extensive testing and appraisal
at their facility, over the next few weeks.
Operating within a 30-40 mile radius of their
Nutts Corner, Crumlin premises, McKinstry Skip Hire has a
fleet of over 500 skips, 50 roll-on-off bins supported by
eight skip trucks and four roll-on-off lorries. In addition,
the company has diversified into dumper and excavator hire
and contracts out a special 38 tonner Renault scrap metals
transporter and operates another 38 tonner Renault tug-and-low-loader
combination - which is busy handling the transportation of
excavators and other heavy construction plant throughout Northern
Ireland.
The business now employs 34 personnel and is
also extremely well-known as a sponsor and supporter of track
superbike and road racing motorcycles - as well as stock-cars.
In fact, covering most of the wallspace in the company's main
office, is a wonderful selection of action shots showing various
bikes and stock-cars proudly displaying the McKinstry name
- with Bruce Anstey and Keith Stewart among the well-known
winning riders recently and currently sponsored by the company.
In the order of 100,000 tonnes of building waste
goes through the McKinstry waste management system during
the year and - using a combination of shredders, a trommel
screen, a "blower" density separator, overband magnet and
a modern picking station - around 1200 tonnes of saleable
material (including 500 tonnes of fines) is extracted on a
weekly basis. The reclamation systems in place effectively
reduce the volume of waste to landfill by some 60%, which
has the dual benefits of diverting material from landfill
and producing reusable materials for sale to a loyal customer
base in the region.
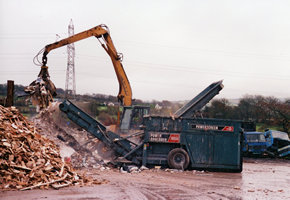
Powershredder 1800
|
On arrival at McKinstry's site, the building
waste is pre-sorted to remove the larger pieces of scrap
metal, timber, boulders, etc. Wheeled loaders stockpile
the sorted material for pre-shredding - carried out almost
non-stop by a Powerscreen Powershredder 1800, fed by a
wheeled Case excavator with long-reach industrial stick
and five-tyne grab. |
This powerful shredder prepares the raw materials for the
next stage, which is screening and separating by a Powerscreen
Trommel 615LL - fed by the loading shovels. This trommel is
housed inside a purpose-built shed with the tail fines conveyor
stockpiling through an aperture in the wall, while the oversize
material is conveyed via a Powerscreen TR Blower, to remove
lightweight materials such as paper, PVC and polystyrene -
and then conveyed directly to the covered picking station.
Here, four sorting stages select and stockpile rubble, timber,
cardboard and plastics along the 12 metres long conveyor belt
and, at the end of the process, ferrous metals are removed
by an overband magnet conveyor. The bins constructed below
the overhead picking station are all designed to accept "40
yarders" so that materials drop straight into these receptacles,
obviating the need for additional rehandling.
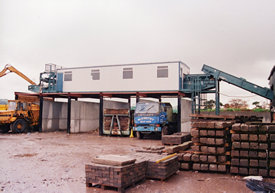
Picking station
|
Powerscreen's picking stations can be customised
to virtually any size to suit customers' applications.
At McKinstry, pickers can be positioned on both sides
of the conveyor and, for enhanced working conditions,
the fully enclosed cabin has heating and lighting. Four
discharge chutes are positioned on both sides of the 12m
long conveyor for convenient "binning" of materials in
their respective stockpiles. |
The reclaimed materials are converted into a multitude of
saleable products for McKinstry. The fines are predominantly
used at both public and private sector landfill sites for
"blinding" between strata of waste material within the cells.
Clean timber, which is stored under cover for temperature
and humidity control, is shredded for onward sale to chipboard
and MDF manufacturers, while the remaining wood products are
used for industrial heating boiler fuels and - in a recent
innovative development by McKinstry - shredded to smaller
sizes and used as cattle bedding in outdoor corrals. Here
3-4 metre-depths are spread, serving as an ideal dry, warm
and easily replaceable "green" outdoor surfacing for both
beef and dairy herds during the winter months. Rubble is transported
all over the region where it is used on building projects,
for temporary haul roads and as general hardcore substrate.
The Powershredder 1800 produces a consistent and uniform
material sizing using a range of toolheads to match, is quiet
in operation and has a low dust emission level. Automatic
and fixed reverse shafts that are easy to replace, makes for
easy maintenance and efficient processing of materials. Additionally,
full remote control is available for safe operating distance.
A generously proportioned low loading and tipping hopper allows
the shredder to be fed by conveyor, excavator or loading shovel.
The hydraulically raised discharge conveyor, with chevron
belting, has a discharge height of some 3 metres for good
stockpiling capacity.
The Trommel 615LL is surprisingly compact for its output,
having a 19m� rotating screen area with variable speed control,
a folding tail conveyor for fines and an optimum output of
150-200 tonnes per hour - depending on application and mesh
size. The twin axle unit has hydraulic jacklegs which, with
the hydraulically folding conveyor, greatly improves mobility
and significantly reduces set-up time, should the unit need
to be moved or transported to another site. The low-loading
hopper means that raw material discharge is made easy for
most sizes of loading shovel or excavator.
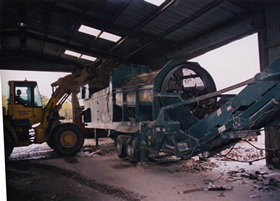
Trommel 615LL
|
The Trommel 615LL is compatible with all Powerscreen
equipment and, therefore, can form an integral component
in a screening, washing and stockpiling installation.
Power is usually provided by a diesel engine, although
electric motors are available as an option - and all
trommel hydraulics are protected by an automatic shut-down
system.
|
A conveniently located control panel provides finger-tip
management of all machine functions. In the McKinstry set-up,
the Trommel 615LL has an hydraulic take-off to provide all
the power for the conveyor in the picking station and its
3m long inclined feed conveyor - both of which have infinitely
variable speeds.
The TR Blower removes light materials, which are caught in
a net and then "skipped". Products from this process include
recyclable paper - which can be baled and sold on for pulping
- and other light waste for incineration or landfill. The
heavier materials then pass up a feed conveyor to the elevated
Picking Station conveyor for hand removal and chute discharge
for disposal or reclamation.
For further information, contact:
Nicola Killen
Powerscreen
Tel: +44 (0)28 87 740701
Fax: +44 (0) 28 87 747231
e-mail: [email protected]
|
�
Press contact:
Chris Davis
Interface Marketing
Tel/Fax: +44 (0) 1483 730493
e-mail: [email protected]
�
|
�
�
�
�
�
�
�
�
�
|